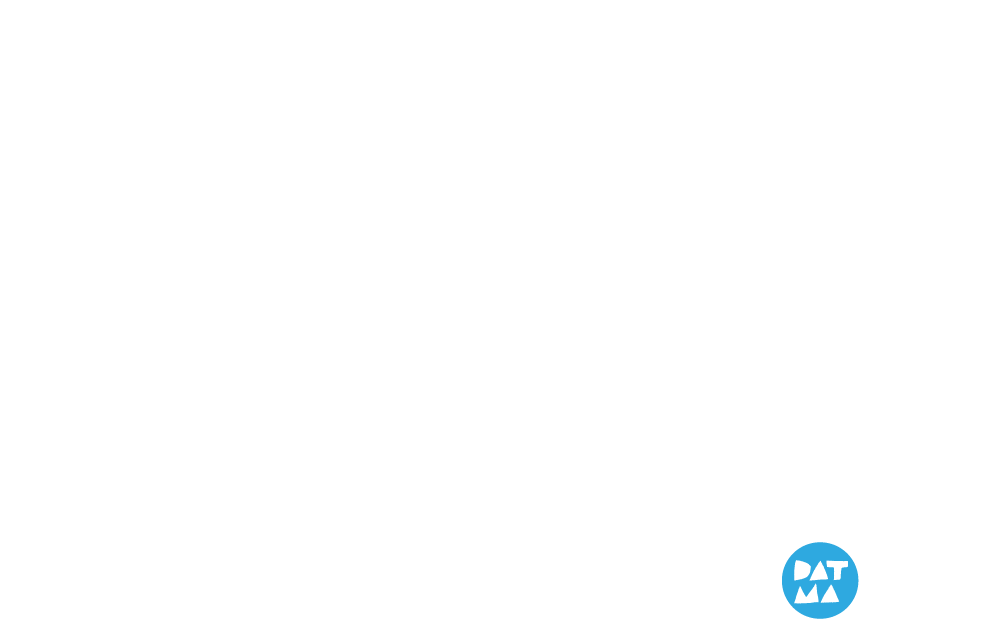
Shelter: Flexible Fibers and Sustainable Solutions
Flexible Fibers & Sustainable Solutions presents three modern approaches to the concept of shelter from Jordan, Korea, and the United States. Through community engagement and the building process, developments of new structural fabrics and spatial design have been created. Each work explores the fabrication of dwellings with unique materials that have resulted in striking architectural productions.
The exhibition features Do Ho Suh’s fabric architecture sculpture, exploring identity, migration, and memory; Abeer Seikaly’s work with Bedouin textile traditions and new structural fabrics; and one of the largest bio-plastic 3D-printed structures to date from Rael San Fratello. These works and the processes behind their creation demonstrate how new technologies weave together unique materials and innovations to evolve our vision of home.
Do Ho Suh
Do Ho Suh works across various media, creating drawings, film, and sculptural works that confront questions of home, physical space, displacement, memory, individuality, and collectivity. Suh is best known for his fabric sculptures that reconstruct to scale his former homes in Korea, Rhode Island, Berlin, London, and New York. He is particularly interested in domestic space and the way the concept of home can be articulated through architecture that has a specific location, form, and history.
Suh received a B.F.A. in painting from Rhode Island School of Design and an M.F.A. in sculpture from Yale University. His work is in numerous international public and private collections, with recent solo exhibitions at Bloomberg SPACE, London, United Kingdom and Los Angeles County Museum of Art. View more of his work at www.lehmannmaupin.com/artists/do-ho-suh.
Hub-1, Entrance, 260-7, Sungbook-Dong, Sungboo-Ku, Seoul, Korea, 2018
Polyester fabric and stainless steel
Do Ho Suh’s delicate fabric sculptures depict rooms, thresholds, and passageways from the artist’s former homes. The sculpture here represents the entryway from the artist’s childhood home in South Korea; reproduced in actual size, with doorknobs, molding, and outlets crafted and sewn in precise detail. Speaking about his connection to home and the broader theme of migration, the artist has stated: “I consider migration to be a process, not something that happens overnight. Each step of the process is like crossing another threshold.” Suh reconfigures memories of home across both time and space for the viewer to experience first-hand, as they retrace the artist’s footsteps through these intimate domestic spaces he once called home.
Tangled Man, 2019
Thread embedded in handmade cotton paper
Do Ho Suh creates his fine thread drawings with a technique he developed during his first residency in 2010 at the Singapore Tyler Print Institute, a creative space for conceptual developments in print and paper. Suh first embroiders his drawing on a gelatine tissue, then lays them down on a wet handmade cotton paper. While the gelatine paper dissolves in water, bits of transferred thread are left behind and bind into the paper fibers to create the final drawing.
Rael San Fratello
Ronald Rael and Virginia San Fratello formed their socially driven design studio to explore and teach new methods of creative architecture. Their team works with both recycled and natural materials to create 3D-printed large scale structures, ‘earth architecture’, interactive installations, and more. Rael San Fratello’s collaborative workshops challenge architects, artists, designers, and engineers to address the untapped potential of materials in the 3D-printing realm.
In 2020, the Pink Borderwall Teeter Totters installed on the border between the USA and Mexico, designed by Rael and San Fratello, was awarded the Beasley Design of the Year Award. Their work is widely published and included in the permanent collections of institutions such as The Museum of Modern Art in New York, The Cooper Hewitt Smithsonian Design Museum, and The London Design Museum. Explore more of their innovations at www.rael-sanfratello.com.
Star Lounge, 2015
3D-printed Polylactic Acid
As one of the largest PLA based 3D printed structures built to date, Star Lounge demonstrates the architectural potential of 3D printing, particularly using the small MakerBot Replicator 2 Desktop 3D printers. Composed of 2073 hexagonal blocks, the structure is printed in various translucent colors that correspond to a particular block type. The Star Lounge illustrates the feasibility of prefabricating 3D printed panels for architectural assembly, and opens the door to creating 3D printed environments, walls, ceilings, partitions and cladding in building construction.
Ronald Rael, Virginia San Fratello, and Mona Ghandi, designed the structure in their Oakland studio and the components were printed and assembled by Bold Machines in their Brooklyn, NY headquarters.
Abeer Seikaly
Abeer Seikaly is a Jordanian Palestinian interdisciplinary creative thinker and maker working across architecture, design, fine art, and cultural production. Through her work, she shares information about ancient cultures we would not have known or is commonly understood by archeologists. Taking woven structures to create tent forms that are foldable, her works are meant to help displaced and unsheltered people.
After receiving her BArch and BFA from the Rhode Island School of Design in 2002, Seikaly won The Rug Company’s 2012 Middle East Wallhanging Design Competition, and was awarded the international Lexus Design Award for a performative structural system, “Weaving a Home.” In 2015, she co-founded and co-directed Amman Design Week. Her works have been exhibited at the Museum of Modern Art (MoMA) in New York, the Museum of Applied Arts (MAK) in Vienna, and the Stedelijk Museum in Amsterdam. Explore more of her work at www.abeerseikaly.com.
Weaving a Home, 2013 – present
Abeer Seikaly works with Bedouin communities to reinterpret Jordan’s built environment. Her conceptual emergency shelter, Weaving A Home, explores the social implications of creating homes for displaced communities. The design received the international Lexus Design Award in 2013, and has gone through multiple phases since its inception to this day.
The collapsible structural fabric shelter can adapt to various climates, while also providing the comforts of contemporary life such as heat, running water, and solar electricity. Composed of high-strength plastic tubing molded into sine-wave curves and woven into a stretchable fabric membrane, the system creates a technical, structural fabric that expands and contracts for mobility.
Rendered Digital Artworks
New Bedford Textile History
New Bedford was among the leading cotton textile centers in the United States during the early 20th century. At its peak in production around 1920, the city had over 70 textile mills, operated by 28 establishments with over 3.7 million spindles. There are currently about 18 mills left in the city today. New Bedford no longer has any working looms, but further north, in Lowell, 80 power looms at the Boot Mills Museum still produce fabric each day.
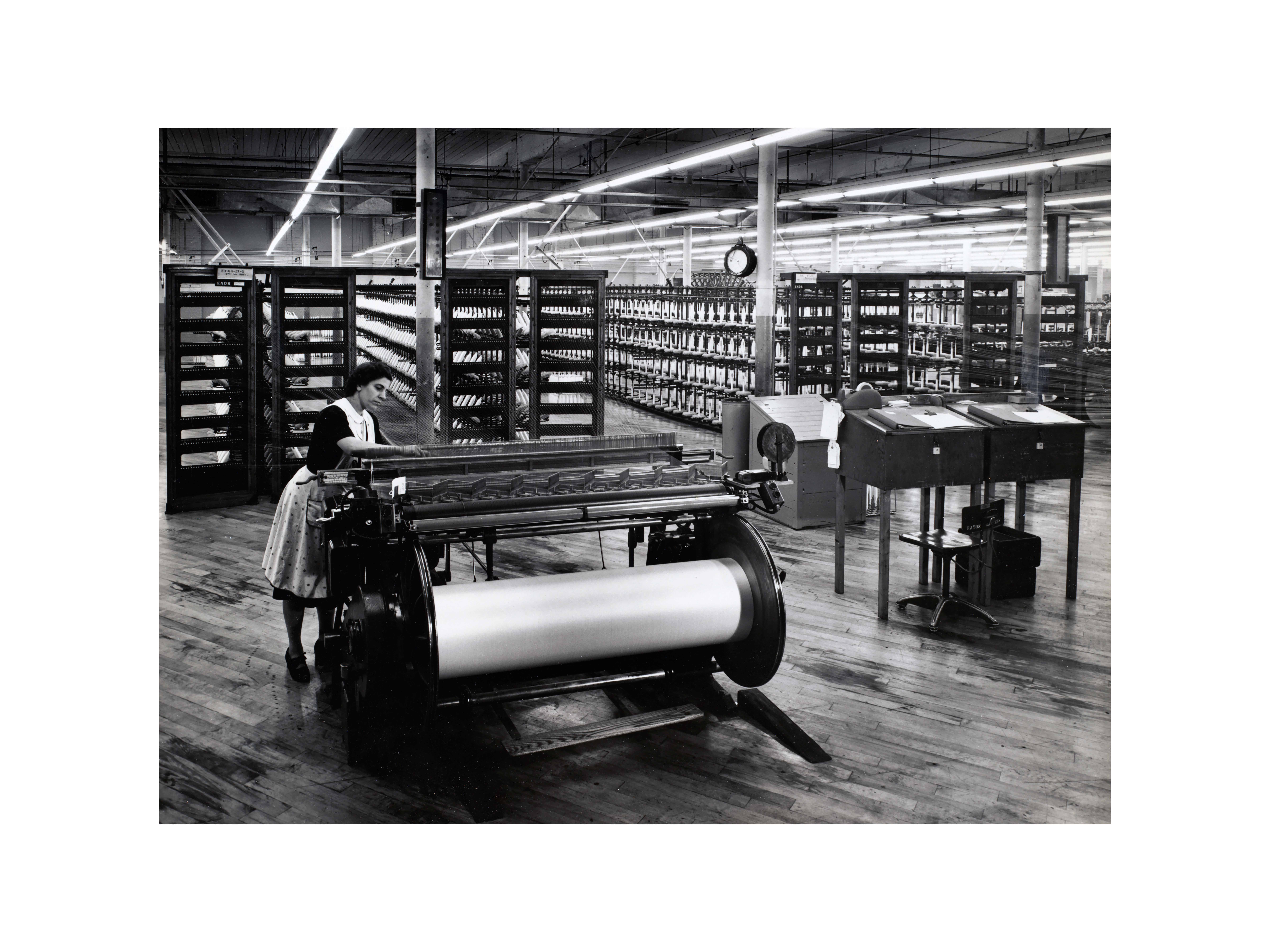
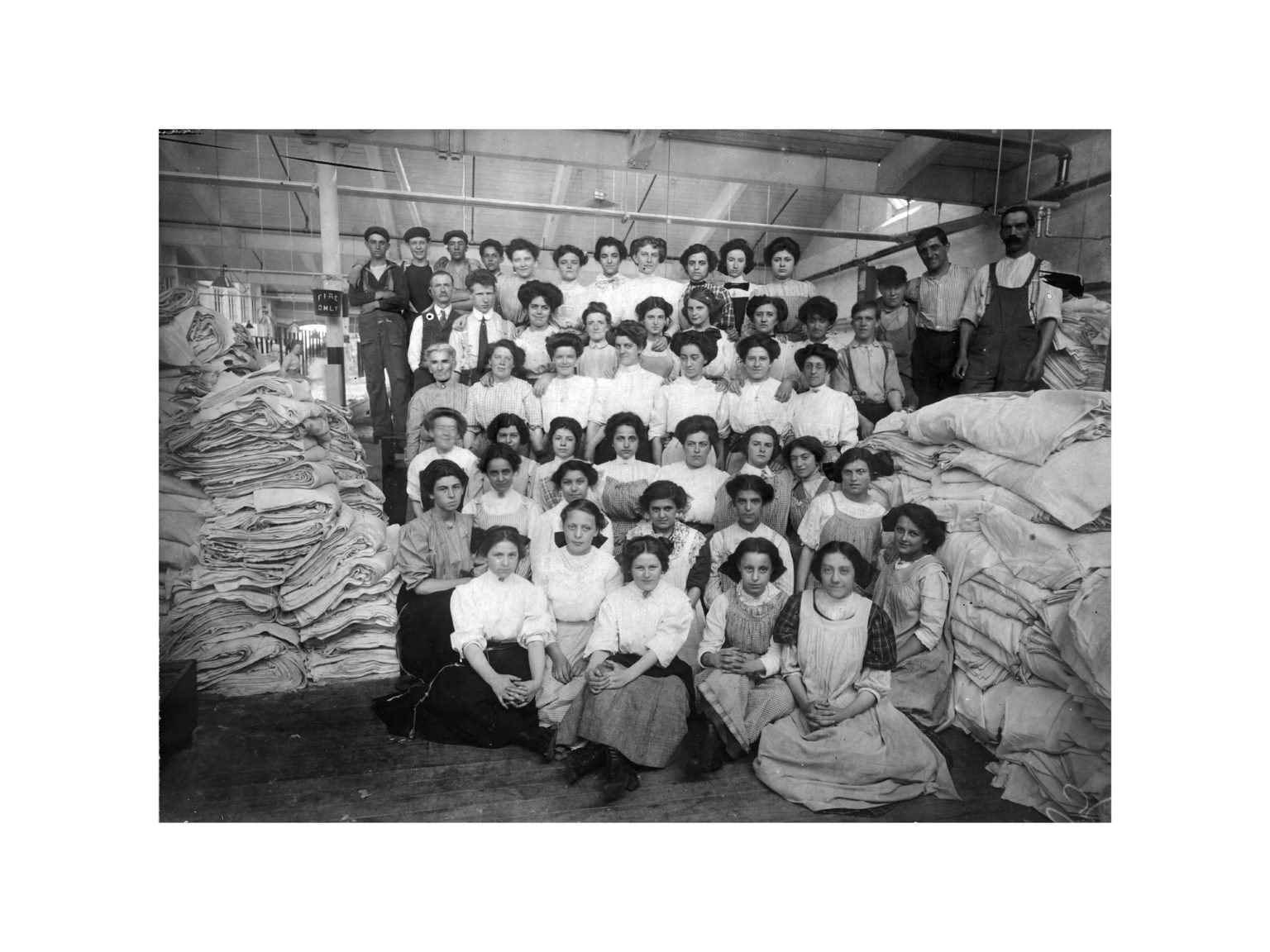
Photographs courtesy of the New Bedford Free Public Library
Events
DATMA Design Days: Eco Art!
DATMA Design Days: Eco Art! 4:00 – 6pm Eco-Friendly Art is an all-ages art project activity where kids and families can explore the importance of recycling and waste reduction, all while transforming discarded plastics and other materials into eco-friendly masterpieces. This free interactive event is for families and kids all ages.